Introduction to Production Casing
In the vast and intricate world of oil and gas extraction, there exists a crucial element that often goes unnoticed by those outside the industry, yet it stands as a sentinel of safety, integrity, and efficiency deep below the Earth's surface. Production casing is the unsung guardian of oil and gas wells, silently ensuring the extraction of hydrocarbons from the depths of the Earth while preventing environmental contamination and maintaining the structural integrity of the wellbore.
Whether you are an industry veteran seeking to refresh your knowledge or a curious newcomer eager to grasp the inner workings of oil and gas wells, this exploration into production casing will equip you with essential insights and best practices that underscore its vital role in the energy sector. So, let's dive deep into the world of production casing, where steel meets stone, and the pursuit of energy resources meets the pursuit of environmental stewardship and safety.
What is Production Casing?
Production casing, in the context of oil and gas wells, is a robust and impermeable steel pipe that lines the wellbore, sealing it off from the surrounding geological formations. Its primary function is to serve as a protective barrier, containing the reservoir fluids, such as crude oil and natural gas, within the wellbore while simultaneously preventing any unwanted fluids or contaminants from entering the formation. Essentially, production casing acts as the final defense against the potential escape of hydrocarbons into the environment and ensures the safe and efficient extraction of valuable resources.
Components of Production Casing
Production casing systems are composed of several key elements working in harmony to ensure their effectiveness. Firstly, the casing pipes themselves form the backbone of this system, with their size, thickness, and metallurgy carefully chosen to withstand the immense pressures and corrosive elements found deep underground. Cementing plays a critical role as well, creating a secure bond between the casing and the surrounding geological formations. Additionally, various casing accessories, such as centralizers, float equipment, and liner hangers, are strategically placed to enhance casing integrity and ensure the proper functioning of the wellbore throughout its operational life.
Role of Production Casing in Well Integrity
Production casing serves a dual role in safeguarding well integrity. Its primary role involves acting as a primary barrier, containing reservoir fluids and isolating different geological zones within the well. This prevents cross-contamination between formations and ensures the efficient production of hydrocarbons. The casing also plays a secondary role by providing protection against corrosive elements, mechanical stresses, and geological instabilities. It acts as a robust outer shield, preserving the long-term stability and safety of the well. In essence, production casing is the guardian that ensures the well's health and longevity, both economically and environmentally.
Casing Size Selection
The selection of the appropriate casing size is a critical decision in the design of oil and gas wells. It's not a one-size-fits-all scenario; rather, it depends on various factors like reservoir characteristics, well depth, and the anticipated downhole conditions. A well-designed casing size should not only accommodate the tubing and production equipment but also provide adequate structural support and fluid containment capacity. A balance between cost-effectiveness and performance is crucial, as overly large casings can be expensive and may impede production efficiency, while undersized casings can compromise well integrity.
Casing Material
The choice of casing material is another pivotal design consideration. Steel is the most commonly used material due to its exceptional strength and corrosion resistance. However, the selection of steel alloy and grade should align with the downhole environment, as corrosive substances present in some reservoirs can lead to casing degradation over time. In certain situations, non-metallic or composite materials may be employed to mitigate corrosion risks. The casing material choice should also adhere to industry standards and regulations.
Cementing Techniques
Proper cementing of the casing is essential for achieving well integrity and zonal isolation. Cement serves as a barrier between the casing and the surrounding geological formations, preventing the migration of fluids and gases. The cementing process involves a careful blend of materials and precise execution, considering factors such as slurry density, setting time, and temperature conditions. Effective cementing is crucial not only for well safety but also for optimal reservoir production.
Casing Accessories
Casing accessories, including centralizers, float equipment, and liner hangers, play a critical role in the casing design. Centralizers ensure the uniform placement of the casing within the wellbore, preventing eccentricity and ensuring even cement distribution. Float equipment assists in the placement of cement and prevents backflow. Liner hangers are used to suspend liner strings within the casing and support the weight of the production tubing. The selection and installation of these accessories must align with well-specific requirements to enhance casing integrity and overall well performance.
Wellbore Pressure Management
Managing wellbore pressure is a fundamental aspect of casing design. The casing must be able to withstand the pressures exerted by the reservoir fluids without deformation or failure. To achieve this, engineers must calculate and consider factors like formation pressure, reservoir depth, and wellbore configuration when designing the casing. A well-designed casing program will include contingency plans for pressure fluctuations during drilling, production, and well maintenance operations, ensuring the overall integrity of the well throughout its lifespan.
Challenges and Solutions
1. Casing Failures:Oil and gas wells are subject to various stresses and environmental factors that can lead to casing failures. Corrosion, for instance, can gradually eat away at the casing's metal, compromising its integrity. In such cases, operators must employ advanced corrosion-resistant materials and coatings, as well as corrosion inhibitors, to extend casing lifespan. Additionally, proper cementing and casing centralization can prevent casing deformation and subsequent failures. Moreover, understanding the geological conditions in which a well is drilled is essential, as different formations can exert unique pressures on the casing, requiring tailored solutions.
2. Remedial Actions:When casing issues arise, it's crucial to have well-defined remedial procedures in place. Casing repair techniques involve repairing or reinforcing the damaged sections to restore integrity. For more severe problems, such as casing breaches, plug and abandonment procedures may be necessary to safely close off the well. The choice between remedial actions depends on the severity of the issue, well economics, and environmental concerns. Modern technologies, like advanced cements and wellbore instruments, offer innovative solutions for addressing casing problems efficiently.
3. Advancements in Casing Technologies:The oil and gas industry continually evolves, and so does the technology used in well construction. Recent advancements in casing technologies have significantly improved well integrity and operational efficiency. Innovations in materials, such as high-strength steels and composite casings, enhance durability and corrosion resistance. Smart casing technologies equipped with sensors and real-time data transmission allow for continuous monitoring of well conditions, enabling rapid response to potential issues. These innovations are instrumental in mitigating challenges and maintaining the reliability of production casing systems in modern drilling operations.
Maintenance and Monitoring
1. Routine Inspections:
Routine inspections are the cornerstone of ensuring the long-term reliability and performance of production casing systems. These scheduled assessments involve visual examinations and measurements of casing components, such as checking for signs of corrosion, wear and tear, or deformation. Through routine inspections, operators can detect potential issues early, allowing for timely interventions to prevent more significant problems down the line. These proactive measures not only ensure well integrity but also contribute to cost-effective operations and environmental protection.
2. Integrity Testing:
Integrity testing is a critical aspect of maintaining production casing. It involves comprehensive assessments aimed at verifying the soundness of the casing and the cement bond. Various integrity testing methods are employed, including pressure testing, electromagnetic inspection tools, and acoustic measurements. These tests help identify any weaknesses, leaks, or integrity breaches in the casing system. By periodically subjecting production casing to rigorous integrity tests, operators can make informed decisions about when and how to perform necessary repairs or replacements, ultimately safeguarding the well and its surroundings.
3. Well Abandonment:
Well abandonment marks the end of a well's productive life, and it's a process that requires careful planning and execution. Production casing plays a pivotal role in this phase, as it must be properly plugged and abandoned to prevent any potential environmental hazards. The casing is often cut and sealed at various depths, with specialized cement plugs used to isolate different formations and permanently seal the wellbore. This ensures that hydrocarbons or other substances cannot migrate to the surface or contaminate groundwater. Well abandonment procedures must adhere to regulatory requirements and industry best practices to protect the environment and public safety, making it a critical aspect of maintenance and monitoring in the life cycle of a well.
Conclusion
Production casing stands as an embodiment of the industry's commitment to safety, integrity, and environmental responsibility. It acts as both a sentinel and a shield, safeguarding our planet's delicate ecosystems while allowing us to harness the energy that powers our modern world. In this ever-evolving industry, staying informed about best practices, innovations, and regulatory standards is key. We encourage you to continue your journey of knowledge, for it is through this collective effort that we not only secure our energy future but also preserve the planet for generations to come.
Popular Articles
Expand your knowledge with these insightful blog posts.
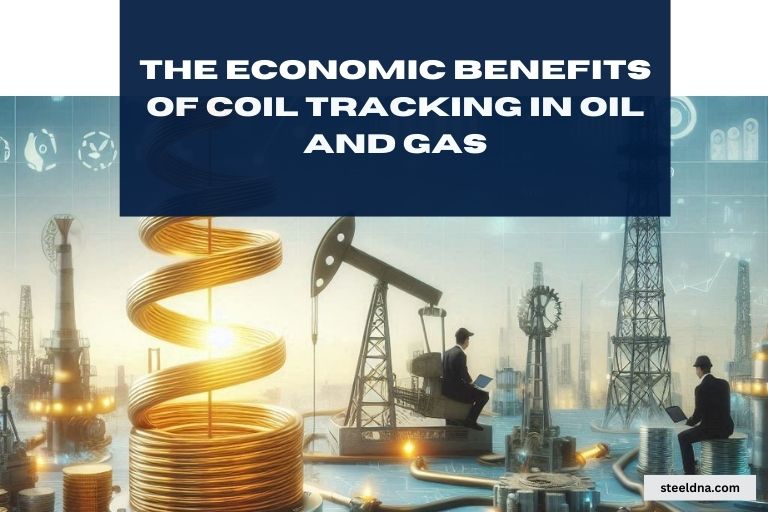
The Economic Benefits of Coil Tracking in Oil and Gas
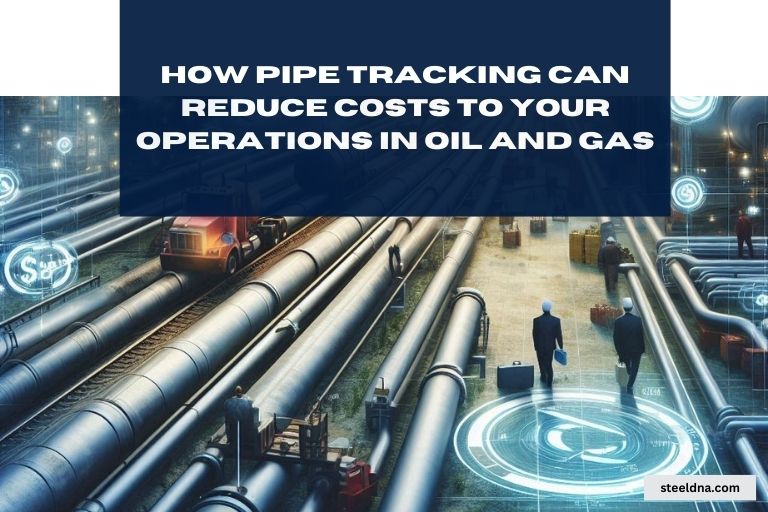
How Pipe Tracking Can Reduce Costs to your Operations in Oil and Gas
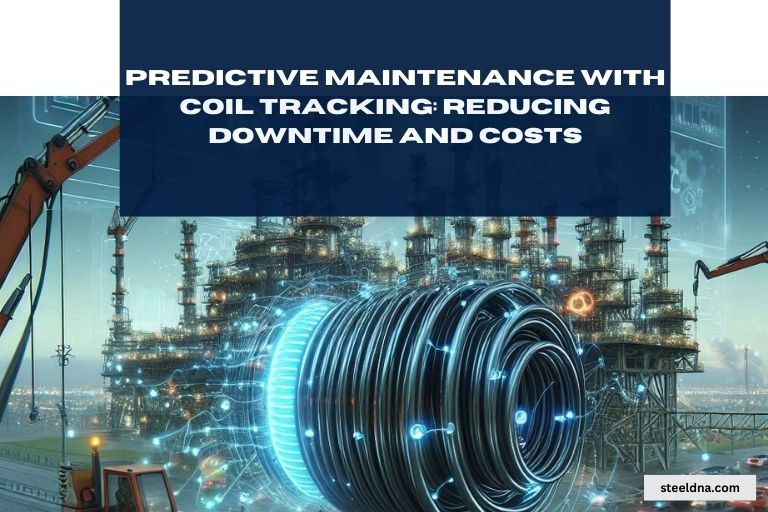
Predictive Maintenance with Coil Tracking: Reducing Downtime and Costs
Subscribe to our Blog
Welcome to our blog! Stay updated with the latest industry trends, tips, and insights. Subscribe now to never miss a post or contact us for collaborations and guest post opportunities.