Introduction
At its core, the maintenance practices employed to uphold asset integrity are pivotal in ensuring operational continuity and mitigating risks inherent to the industry. Yet, this domain is rife with challenges, from aging infrastructure to regulatory compliance demands, which necessitate a systematic approach to maintenance. Standardization emerges as a beacon of efficiency, offering a structured framework to navigate these complexities and fortify asset reliability.
Understanding Asset Integrity
- Definition of Asset Integrity- Asset integrity in the oil and gas industry revolves around the reliable functionality and safety of equipment, infrastructure, and facilities. It encompasses ensuring that all components within the operational environment function as intended, maintaining their structural and functional integrity over time. Asset is an active pursuit involving rigorous monitoring, maintenance, and risk management to prevent failures that could lead to safety incidents, environmental damage, or operational downtime.
- Importance of Asset Integrity- The industry operates in challenging environments, including offshore rigs, pipelines spanning vast distances, and processing facilities handling volatile substances. Any compromise in asset integrity can lead to catastrophic consequences, such as spills, explosions, or equipment failures, with far-reaching impacts on human lives, the environment, and company reputation. Therefore, ensuring asset integrity is not just a matter of compliance but a fundamental aspect of responsible and sustainable operations in the oil and gas industry.
- Consequences of Asset Integrity Failures- Beyond the immediate risks to personnel and the environment, such failures can disrupt operations, leading to costly downtime, production losses, and regulatory penalties. Moreover, incidents tarnish the reputation of companies involved, eroding trust among stakeholders and investors. The aftermath of asset integrity failures often involves extensive cleanup efforts, legal battles, and long-term environmental remediation, underscoring the importance of proactive measures to prevent such events.
The Role of Maintenance Practices
- Explanation of maintenance practices in maintaining asset integrity- Maintenance practices play a pivotal role in upholding asset integrity within the oil and gas industry. They encompass a range of proactive and reactive strategies aimed at preserving the functionality, reliability, and safety of critical infrastructure. Through regular inspections, servicing, and repairs, maintenance teams ensure that equipment and facilities remain in optimal condition to withstand the rigors of operational demands and environmental factors.
- Different types of maintenance approaches (preventive, predictive, corrective)- Within maintenance strategies, several approaches are employed to address diverse operational needs. Preventive maintenance involves scheduled inspections and servicing to preemptively address potential issues before they escalate into costly failures. Predictive maintenance utilizes data analytics and condition monitoring to anticipate equipment failures and optimize maintenance schedules for maximum efficiency. Corrective maintenance, on the other hand, focuses on addressing issues as they arise, minimizing downtime and mitigating risks to asset integrity.
- Link between effective maintenance practices and operational reliability- Effective maintenance practices are intrinsically linked to operational reliability within the oil and gas sector. By ensuring the timely upkeep of equipment and infrastructure, companies can minimize the likelihood of unplanned downtime and production disruptions. This, in turn, enhances operational continuity, enabling companies to meet production targets and fulfill contractual obligations reliably. Additionally, proactive maintenance efforts contribute to a safer working environment by identifying and rectifying potential hazards before they compromise personnel safety or environmental integrity.
Challenges in Maintenance Practices
- Aging Infrastructure- The aging infrastructure in the oil and gas industry poses a significant challenge to maintenance practices. Equipment and facilities that have been in operation for decades require more frequent and specialized maintenance to ensure continued reliability and safety. Addressing the issues associated with aging infrastructure demands proactive strategies to mitigate the risks of equipment failure and unplanned downtime.
- Harsh Operating Conditions- Oil and gas operations often take place in harsh and remote environments, including offshore platforms, deserts, and Arctic regions. These extreme conditions subject equipment to corrosion, erosion, and mechanical stress, increasing the complexity and frequency of maintenance requirements. Overcoming the challenges posed by harsh operating conditions necessitates the use of durable materials, advanced coatings, and specialized maintenance techniques tailored to specific environmental factors.
- Regulatory Requirements- The oil and gas industry is subject to stringent regulatory requirements aimed at ensuring environmental protection, worker safety, and operational integrity. Compliance with complex and evolving regulations adds layers of complexity to maintenance practices, requiring companies to invest in robust compliance management systems and personnel training. Navigating the regulatory landscape demands a proactive approach to stay abreast of changes and implement effective maintenance strategies that align with regulatory expectations.
- Asset Complexity- The increasing complexity of oil and gas assets, including offshore platforms, refineries, and pipelines, presents challenges for maintenance practices. Modern facilities incorporate advanced technology, automation, and interconnected systems, requiring specialized expertise and resources for maintenance and troubleshooting. Managing the complexity of assets requires comprehensive asset management strategies, including risk assessment, condition monitoring, and lifecycle planning, to ensure optimal performance and longevity.
Benefits of Standardizing Maintenance Practices
- Consistency- Standardizing maintenance practices ensures uniformity across different facilities and operations within the oil and gas industry. This consistency streamlines processes and reduces the likelihood of errors or inconsistencies in maintenance procedures. By adhering to standardized practices, companies can maintain a high level of reliability and predictability in their maintenance operations, ultimately contributing to improved asset integrity and operational efficiency.
- Efficiency- Standardized maintenance practices enable oil and gas companies to optimize their resource allocation and workflow management. With clear and well-defined procedures in place, maintenance activities can be executed more efficiently, reducing downtime and maximizing asset utilization. By eliminating unnecessary variation and confusion in maintenance tasks, standardization allows teams to focus their efforts on tasks that add the most value, ultimately enhancing overall productivity and cost-effectiveness.
- Compliance- In the highly regulated environment of the oil and gas industry, adherence to regulatory requirements is paramount. Standardizing maintenance practices ensures that companies consistently meet and exceed regulatory standards for asset integrity, safety, and environmental protection. By aligning maintenance protocols with regulatory expectations, organizations can mitigate compliance risks and demonstrate a commitment to responsible operations, safeguarding their reputation and minimizing the potential for regulatory penalties or sanctions.
- Risk Reduction- Effective maintenance practices are essential for mitigating risks associated with asset integrity failures, such as equipment malfunctions, leaks, or accidents. Standardizing maintenance procedures helps identify and address potential risks proactively, reducing the likelihood of unplanned downtime, incidents, or environmental hazards. By implementing standardized risk assessment methodologies and preventive maintenance schedules, companies can minimize the probability and severity of asset integrity issues, enhancing overall operational resilience and continuity.
- Continuous Improvement- Standardizing maintenance practices facilitates a culture of continuous improvement within oil and gas organizations. By establishing standardized metrics, benchmarks, and performance indicators, companies can measure the effectiveness of their maintenance activities and identify areas for optimization and innovation. This data-driven approach enables teams to make informed decisions, implement best practices, and adapt to changing operational needs or industry trends, driving ongoing enhancements in asset integrity, reliability, and overall performance.
Implementing Standardized Maintenance Practices
- Establishing Clear Maintenance Procedures and Protocols- Oil and gas companies must prioritize the establishment of clear maintenance procedures and protocols. This involves defining step-by-step guidelines for conducting various maintenance activities, including inspections, repairs, and replacements. By clearly outlining these procedures, organizations ensure consistency and accuracy in maintenance tasks across different facilities and operational areas. Clear protocols also facilitate effective communication among maintenance teams, leading to quicker response times and reduced downtime in case of equipment failures or issues.
- Training Personnel on Standardized Procedures and Best Practices- Another critical aspect of implementing standardized maintenance practices is training personnel on these procedures and best practices. This training should cover not only the technical aspects of performing maintenance tasks but also the importance of adhering to standardized protocols for ensuring asset integrity and operational reliability. By investing in comprehensive training programs, companies empower their workforce to execute maintenance activities efficiently and safely, ultimately contributing to improved asset performance and longevity.
- Leveraging Technology and Data Analytics for Predictive Maintenance- Incorporating technology and data analytics into maintenance practices is essential for modern oil and gas operations. By leveraging advanced sensors, monitoring systems, and predictive analytics algorithms, companies can move from reactive to proactive maintenance strategies. Predictive maintenance enables organizations to anticipate equipment failures before they occur, allowing for timely interventions and preventive actions. This not only minimizes unplanned downtime but also extends the lifespan of critical assets, optimizing operational efficiency and reducing overall maintenance costs.
Measuring Success and Continuous Improvement
- Key Performance Indicators (KPIs)- Oil and gas companies track various KPIs to gauge the effectiveness of standardized maintenance practices. Metrics such as mean time between failures (MTBF), mean time to repair (MTTR), and overall equipment effectiveness (OEE) provide valuable insights into asset reliability and performance. By regularly monitoring these KPIs, companies can identify areas for improvement and make data-driven decisions to optimize maintenance strategies.
- Ongoing Monitoring and Evaluation- Continuous monitoring and evaluation are essential for ensuring the long-term success of standardized maintenance practices. Oil and gas companies utilize advanced monitoring tools and systems to track asset health in real-time, enabling proactive maintenance interventions. Regular inspections, audits, and performance reviews help identify potential issues early on and prevent costly downtime or failures. Through ongoing monitoring and evaluation, companies can adapt their maintenance approaches to changing operational conditions and industry requirements.
- Feedback Loops for Improvement- Feedback loops play a crucial role in driving continuous improvement in maintenance practices. Oil and gas companies actively seek feedback from frontline workers, maintenance technicians, and other stakeholders involved in the maintenance process. This feedback helps identify inefficiencies, bottlenecks, and areas for improvement in maintenance procedures. By fostering a culture of continuous improvement and incorporating feedback into decision-making processes, companies can enhance the effectiveness and efficiency of their maintenance practices over time.
Conclusion
Standardizing maintenance serves as a bulwark against the looming threats of operational hazards and ensures the continued reliability of critical infrastructure. By establishing uniform procedures and protocols, companies can fortify their defenses against potential risks, fostering a culture of resilience and reliability.
By prioritizing asset integrity and committing resources towards standardized maintenance practices, organizations can mitigate risks, enhance operational efficiency, and safeguard their reputation. Embracing this proactive stance not only ensures regulatory compliance but also cultivates trust among stakeholders and reinforces the industry's commitment to safety and sustainability.
By fostering a culture of excellence and accountability, companies can nurture operational resilience and adaptability in the face of evolving challenges. Furthermore, by investing in the longevity of assets through standardized maintenance, organizations lay the groundwork for sustainable growth and continued success in a rapidly changing landscape.
Popular Articles
Expand your knowledge with these insightful blog posts.
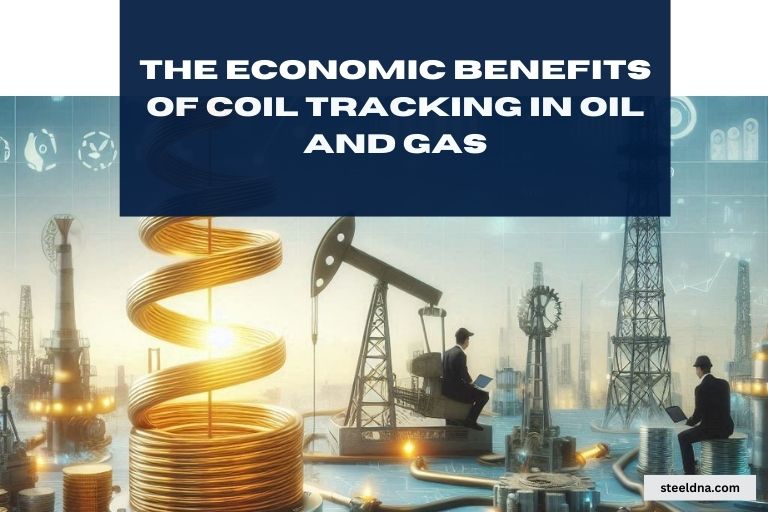
The Economic Benefits of Coil Tracking in Oil and Gas
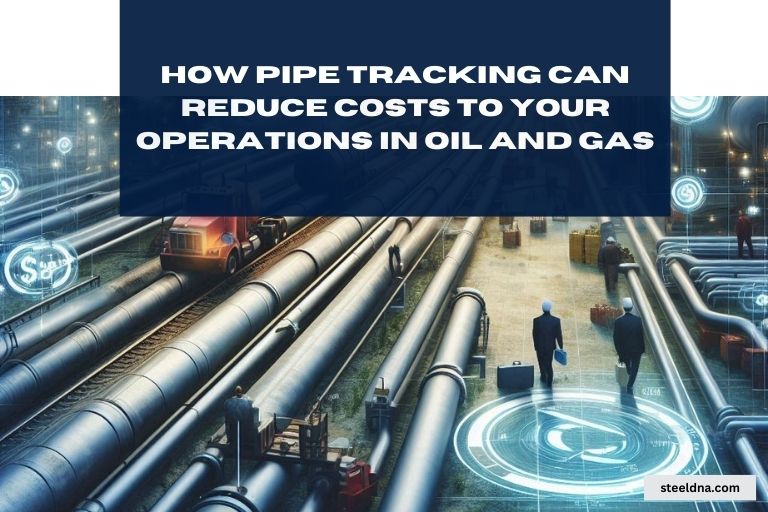
How Pipe Tracking Can Reduce Costs to your Operations in Oil and Gas
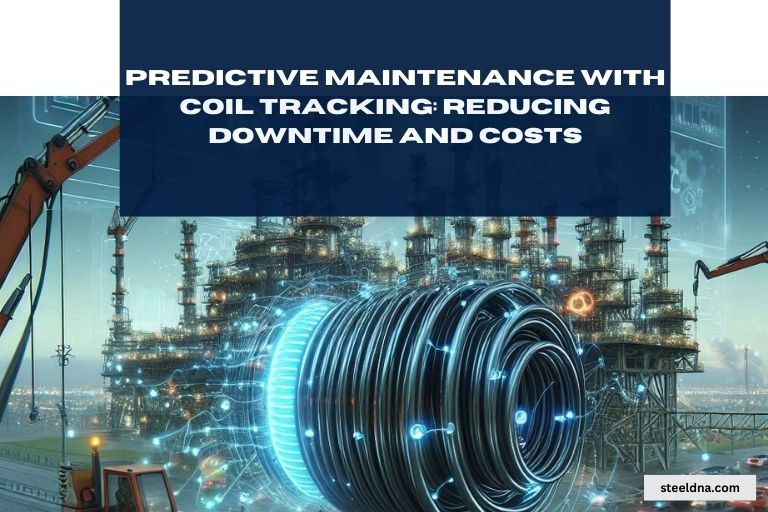
Predictive Maintenance with Coil Tracking: Reducing Downtime and Costs
Subscribe to our Blog
Welcome to our blog! Stay updated with the latest industry trends, tips, and insights. Subscribe now to never miss a post or contact us for collaborations and guest post opportunities.