Introduction
In the oil and gas industry, the regular inspection of equipment serve as vital checkpoints, ensuring that facilities uphold rigorous standards and comply with regulatory requirements. By proactively identifying and addressing potential issues, oil and gas companies can safeguard their personnel, the environment, and their assets. This article delves into the critical importance of conducting regular equipment inspections in oil and gas facilities, examining their role in enhancing safety, integrity, and regulatory compliance within the industry.
Understanding Equipment Inspections
- Definition and Scope of Equipment Inspections- Equipment inspections involve a systematic assessment of machinery, tools, and infrastructure within oil and gas facilities to ensure they meet safety, operational, and regulatory standards. These inspections encompass a wide range of equipment, including pumps, valves, pipelines, and storage tanks, among others. Through detailed examination and testing, inspectors identify potential defects, wear and tear, or deviations from established norms that could compromise safety or performance.
- Types of Equipment Subject to Inspections- Various types of equipment are subject to inspections in oil and gas facilities to maintain operational integrity and safety. This includes mechanical equipment such as compressors, turbines, and generators, as well as electrical systems, instrumentation, and control devices. Additionally, structural components like piping, tanks, and pressure vessels require thorough inspections to ensure they remain structurally sound and leak-free. Inspections also extend to safety systems, fire suppression equipment, and emergency response mechanisms to mitigate risks and protect personnel and the environment.
- Regulatory Requirements and Industry Standards- Equipment inspections in the oil and gas industry are governed by a complex framework of regulatory requirements and industry standards aimed at safeguarding operations, personnel, and the environment. Regulatory bodies, such as the Occupational Safety and Health Administration (OSHA) and the Environmental Protection Agency (EPA), establish mandatory guidelines for equipment inspections to prevent accidents, spills, and emissions. Industry organizations like the American Petroleum Institute (API) and the International Organization for Standardization (ISO) develop voluntary standards and best practices to further enhance safety and operational efficiency. Compliance with these regulations and standards is imperative for oil and gas companies to mitigate risks, ensure compliance, and uphold their social and environmental responsibilities.
Importance of Regular Equipment Inspections
- Ensuring Operational Safety- These inspections help to identify and rectify potential hazards and malfunctions before they escalate into accidents or incidents. By proactively addressing safety concerns through thorough inspections, oil and gas companies can mitigate risks and create a safer working environment for everyone involved.
- Enhancing Asset Integrity- By identifying wear and tear, corrosion, or other forms of deterioration early on, companies can take preventive measures to extend the lifespan of equipment. This not only reduces the likelihood of unexpected failures but also minimizes downtime and production losses, ultimately optimizing operational efficiency.
- Compliance and Regulatory Requirements- Oil and gas facilities must adhere to various regulations governing equipment maintenance and safety protocols. Conducting regular inspections helps companies stay abreast of these regulations, thereby avoiding penalties, fines, and potential legal consequences. Compliance with these standards also fosters trust among stakeholders and demonstrates a commitment to responsible operations.
Best Practices for Conducting Equipment Inspections
- Establishing a Comprehensive Inspection Plan
- Frequency and Schedule- Determine the optimal frequency for inspections based on equipment criticality, operational demands, and regulatory requirements. Create a detailed schedule that accounts for routine, preventive, and periodic inspections to ensure thorough coverage and timely identification of issues.
- Inspection Procedures and Checklists- Develop standardized inspection procedures and checklists tailored to specific equipment types and operational contexts. Clearly outline inspection steps, criteria for assessment, and reporting protocols to streamline the process and maintain consistency across inspections.
- Utilizing Technology and Tools
- Implementing IoT Sensors and Monitoring Systems- Integrate IoT sensors and real-time monitoring systems to collect data on equipment performance, condition, and environmental factors. Leverage advanced analytics to detect anomalies, predict potential failures, and optimize maintenance schedules for proactive interventions.
- Leveraging Data Analytics for Predictive Maintenance- Harness the power of data analytics to analyze inspection data, historical trends, and maintenance records. Identify patterns, correlations, and early warning signs of equipment degradation or failure to enable predictive maintenance strategies that minimize downtime and maximize asset reliability.
- Training and Empowering Personnel
- Ensuring Competency and Skill Development- Provide comprehensive training programs to equip personnel with the knowledge, skills, and competencies required for effective equipment inspections. Offer specialized training on inspection techniques, equipment-specific considerations, and safety protocols to enhance proficiency and confidence among inspection teams.
- Fostering a Culture of Safety and Compliance- Cultivate a workplace culture that prioritizes safety, integrity, and regulatory compliance in all aspects of equipment inspections. Encourage open communication, proactive reporting of hazards or deficiencies, and continuous improvement initiatives to foster a collective commitment to maintaining operational excellence and safeguarding personnel and assets.
Conclusion
Prioritizing regular equipment inspections in oil and gas facilities is paramount for ensuring operational safety, enhancing asset integrity, and maintaining compliance with regulatory standards. By establishing comprehensive inspection plans, utilizing advanced technology, and investing in personnel training, companies can mitigate risks, minimize downtime, and safeguard both personnel and the environment. Through proactive measures and a commitment to excellence, the oil and gas industry can continue to thrive while prioritizing safety, integrity, and sustainability.
Popular Articles
Expand your knowledge with these insightful blog posts.
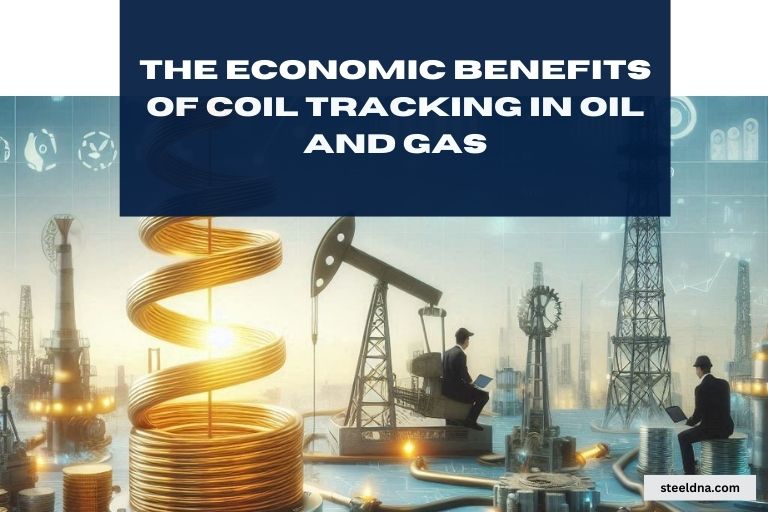
The Economic Benefits of Coil Tracking in Oil and Gas
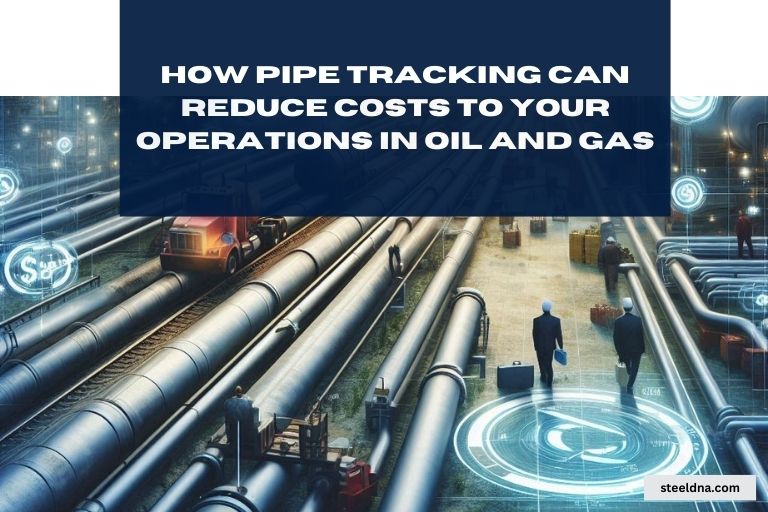
How Pipe Tracking Can Reduce Costs to your Operations in Oil and Gas
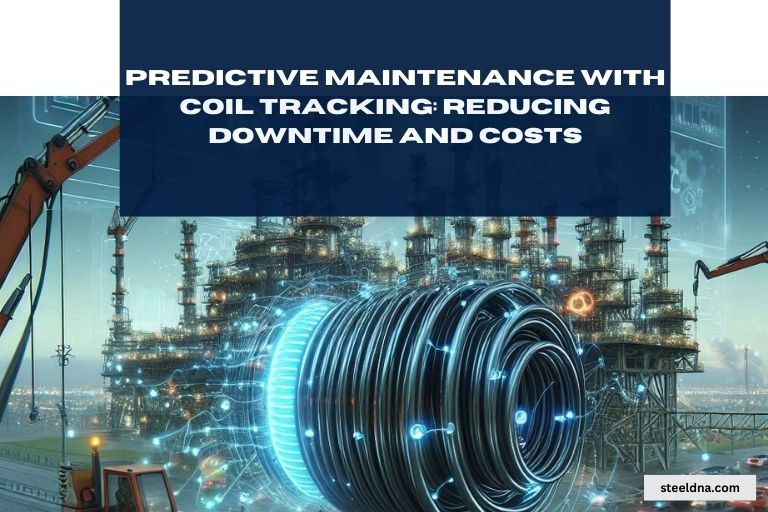
Predictive Maintenance with Coil Tracking: Reducing Downtime and Costs
Subscribe to our Blog
Welcome to our blog! Stay updated with the latest industry trends, tips, and insights. Subscribe now to never miss a post or contact us for collaborations and guest post opportunities.