Introduction to Surface Casing
Surface casing serves as the initial protective barrier in the drilling process, shielding our precious water resources and the environment from potential contamination and ensuring that drilling operations proceed safely and efficiently. Join us as we journey through the depths of surface casing, understanding its importance, challenges, and promising innovations. By the end of this exploration, you will not only comprehend the pivotal role surface casing plays but also recognize the pivotal part you can play in ensuring responsible drilling practices for a sustainable future.
What is Surface Casing?
Surface casing is a critical component in the process of drilling for oil and gas. It serves as the initial protective barrier in a wellbore, situated closest to the surface. The primary function of surface casing is to safeguard the environment and ensure the integrity of the well. By encasing the uppermost section of the well, it prevents the uncontrolled release of drilling fluids, oil, or gas, which could potentially contaminate the surrounding soil and groundwater. Surface casing is typically composed of heavy-duty steel pipes, carefully designed to withstand the challenges posed by the drilling process. Its installation and proper cementing are essential to create a secure barrier that can withstand the pressures and environmental risks associated with drilling activities. Surface casing is a fundamental element of responsible drilling practices, playing a vital role in environmental protection and regulatory compliance.
The Role of Surface Casing in Environmental Protection
Surface casing plays a pivotal role in environmental protection in the context of oil and gas drilling operations. Its primary function is to serve as a robust barrier between the drilling borehole and the surrounding environment. This containment layer is critical for preventing the escape of drilling fluids, which can be laden with harmful chemicals, as well as the unplanned release of oil and gas. By effectively isolating these substances deep within the well, surface casing minimizes the risk of groundwater contamination and soil pollution. In doing so, it helps safeguard ecosystems, drinking water supplies, and nearby communities from the potentially devastating consequences of environmental contamination. Furthermore, adherence to regulatory standards and best practices in surface casing installation is integral to ensuring that drilling operations maintain a responsible and environmentally conscious approach, promoting long-term sustainability in the oil and gas industry.
Surface Casing Installation Process
The surface casing installation process serves multiple essential functions. It begins by determining the appropriate depth for setting the surface casing, which is typically done to secure and protect shallow groundwater aquifers from potential contamination during drilling. Once the depth is determined, the casing is inserted into the wellbore, and cement is pumped down the casing and circulated back up the annulus between the casing and the wellbore. This cementing process not only anchors the casing in place but also forms a barrier that isolates drilling fluids and prevents their migration into the surrounding environment. After the cement has set, the integrity of the casing is rigorously pressure-tested to ensure it can withstand the challenges of drilling and environmental protection. Throughout the surface casing installation process, strict adherence to industry standards and regulatory guidelines is paramount to ensuring the safety of both the drilling operation and the environment.
Surface Casing Standards and Regulations
Surface casing standards and regulations play a pivotal role in ensuring the safe and environmentally responsible execution of oil and gas drilling operations. These guidelines provide essential benchmarks for the design, installation, and maintenance of surface casing. They encompass crucial aspects such as casing material specifications, cementing procedures, pressure testing requirements, and setback distances from environmentally sensitive areas. Compliance with these standards is not only a legal obligation but also a moral imperative to safeguard the environment and protect public health. These regulations vary by region and are often subject to updates, reflecting the industry's evolving understanding of environmental concerns. Staying informed about and adhering to these standards is paramount for drilling companies to mitigate risks, prevent accidents, and maintain the industry's social license to operate.
Advancements in Surface Casing Technology
Advancements in surface casing technology have significantly improved the efficiency, safety, and environmental responsibility of oil and gas drilling operations. Modern surface casing designs incorporate innovative materials and engineering techniques, such as corrosion-resistant alloys and high-strength composite casings, enhancing their longevity and resistance to harsh drilling environments. Furthermore, the integration of real-time monitoring technologies allows drillers to assess the integrity of surface casing more accurately, preventing potential issues and ensuring early detection of anomalies. These technological innovations not only reduce operational risks but also contribute to minimizing environmental impacts by preventing the escape of drilling fluids and hydrocarbons into the surrounding environment. As the industry continues to invest in research and development, surface casing technology will likely play an increasingly pivotal role in ensuring the sustainability and environmental responsibility of drilling operations.
Surface Casing Failures and Remediation
Surface casing failures in oil and gas drilling can lead to significant operational, environmental, and safety issues. These failures may result from a variety of factors, including corrosion, cementing problems, pressure differentials, or mechanical defects. When such failures occur, they can compromise the well's integrity, allowing the migration of fluids, including potentially harmful substances, to the surface or into groundwater. Remediation of surface casing failures is a critical and often complex process. It typically involves well intervention methods like squeezing cement to seal leaks, setting additional casing strings to isolate problem zones, or even abandoning the well entirely in extreme cases. The choice of remediation method depends on the severity and nature of the failure, as well as regulatory and environmental considerations. Effective remediation not only ensures well integrity but also minimizes environmental impact, emphasizing the need for continuous monitoring and maintenance in the oil and gas industry.
Best Practices for Surface Casing
Best practices for surface casing are paramount in ensuring safe and environmentally responsible drilling operations.
- Select the appropriate casing materials and design is fundamental, as it directly affects the casing's integrity and performance.
- Conduct thorough geotechnical surveys and wellbore planning to accurately determine the optimal depth for surface casing installation is crucial.
- Cement and seal the casing properly, followed by rigorous pressure testing, should never be compromised.
- Continuously monitor and assess the casing's condition during drilling operations is essential for early detection of potential issues.
- Adhere to industry standards and environmental regulations, alongside proactive community engagement, is essential for maintaining public trust and minimizing the environmental impact of drilling activities.
Best practices for surface casing underscore the importance of both safety and environmental stewardship in the oil and gas industry.
Conclusion
In the world of oil and gas drilling, surface casing may not always be in the spotlight, but its significance cannot be understated. This unassuming barrier plays a critical role in safeguarding the environment, protecting groundwater, and ensuring the integrity of drilling operations. As we've explored in this blog post, the installation and maintenance of surface casing are not just industry best practices but also legal obligations aimed at minimizing environmental risks.
While technology and innovation are constantly evolving, so too should our commitment to adhering to the highest standards in surface casing design, installation, and maintenance. It is incumbent upon the oil and gas industry to prioritize environmental responsibility, stay informed about evolving regulations, and continue pushing the boundaries of technology to further improve surface casing practices.
Popular Articles
Expand your knowledge with these insightful blog posts.
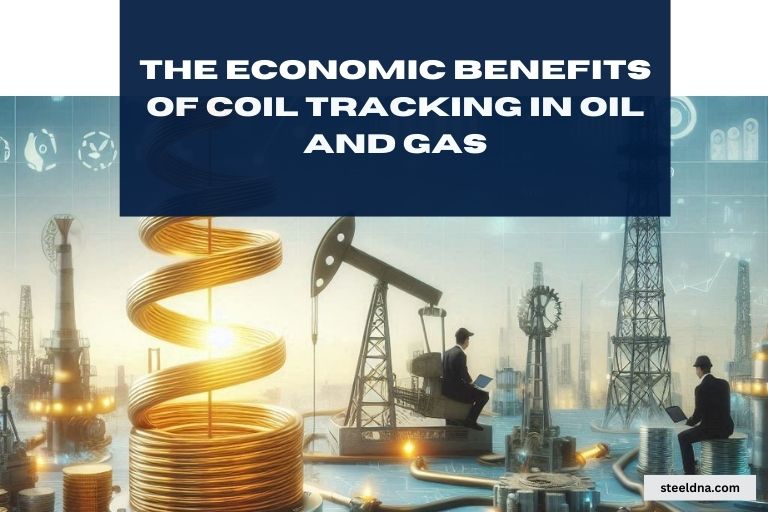
The Economic Benefits of Coil Tracking in Oil and Gas
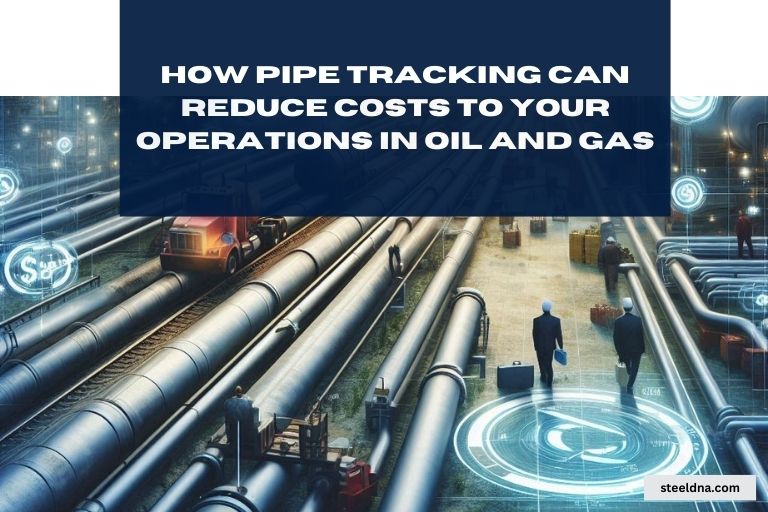
How Pipe Tracking Can Reduce Costs to your Operations in Oil and Gas
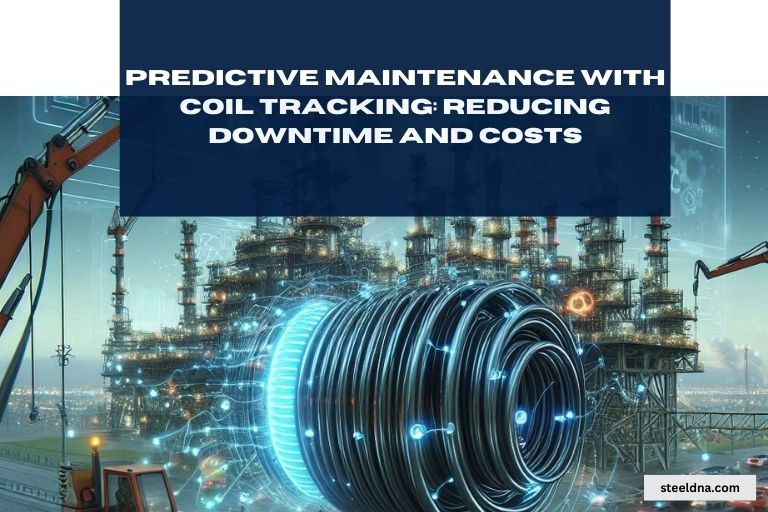
Predictive Maintenance with Coil Tracking: Reducing Downtime and Costs
Subscribe to our Blog
Welcome to our blog! Stay updated with the latest industry trends, tips, and insights. Subscribe now to never miss a post or contact us for collaborations and guest post opportunities.