Introduction to Liners
Liners are an essential but often overlooked component that plays a critical role in maintaining the integrity, safety and efficiency of the entire infrastructure for the oil and gas industry. These unassuming protective barriers, strategically placed within wells, pipelines and crucial structural components, serve as guardians against corrosion, aid in structural support and play a vital role in enhancing operational reliability. From safeguarding against corrosion in drilling operations to ensuring the structural stability of wellbores, these unobtrusive elements serve as the backbone of safety and efficiency in the oil and gas sector.
This blog post aims to delve deep into the world of liners exploring their varied types, functions, challenges faced in their implementation and the innovative solutions that are revolutionizing their application. Moreover, it highlights the numerous benefits they bring to the table, including enhanced safety, improved efficiency and a sustained focus on environmental responsibility.
Understanding the Primary Functions of Liners
- Containment and Protection: Liners primarily serve the crucial role of containment and protection. They act as a barrier, preventing the escape of hazardous substances such as oil, gas or other fluids. Liners are instrumental in ensuring the containment of these substances within the designated areas, reducing the risk of environmental contamination or spillage. Additionally, they shield the infrastructure, such as well casings and pipelines, from corrosion, erosion and structural damage caused by harsh operating conditions, thereby extending the lifespan of the equipment and maintaining operational integrity.
- Corrosion Prevention and Structural Support: One of the critical functions of liners is to combat corrosion and provide structural support. In an industry where equipment is constantly exposed to corrosive elements, liners offer a protective layer, shielding the internal components from chemical reactions and degradation. By preventing corrosion, liners contribute significantly to the longevity and reliability of the infrastructure, ensuring the safety and efficiency of oil and gas operations. They also provide structural support to maintain the integrity of well casings, preventing collapse or deformation under high pressure or extreme conditions, which is essential for the overall stability of the extraction and transportation processes.
- Enhancing Operational Efficiency: Liners play a pivotal role in optimizing operational efficiency within the oil and gas sector. They assist in maintaining the desired pressure levels, facilitating smooth fluid flow, and reducing operational complexities. Properly installed liners improve the wellbore integrity, minimizing obstructions and blockages, thus enhancing the overall productivity and efficiency of the extraction, drilling, and transportation processes. Their ability to create a consistent and reliable environment within the infrastructure contributes to streamlined operations, ensuring a continuous and more predictable flow of oil or gas.
Benefits of Liners
- Improved Safety Measures and Risk Mitigation: Liners play a crucial role in ensuring enhanced safety within the oil and gas sector. By acting as protective barriers, they prevent leaks, corrosion, and structural failures, reducing the risk of environmental hazards and accidents. They provide an additional layer of defense, especially in critical areas such as wells and pipelines, shielding against potential ruptures and leaks that could lead to harmful spills or accidents. Liners act as a protective shield, mitigating the risk of environmental contamination and ensuring the safety of both the workforce and surrounding communities.
- Enhanced Operational Efficiency and Productivity: The strategic use of liners significantly contributes to the operational efficiency of oil and gas processes. By preventing corrosion, maintaining well integrity, and improving flow efficiency, liners aid in optimizing production rates and reducing downtime for maintenance. They help maintain the structural integrity of wells, pipelines, and storage facilities, ensuring continuous and reliable operation. Moreover, specific liner types, such as casing liners and tubing liners, facilitate smoother fluid transport, supporting enhanced productivity within extraction, transportation, and storage processes.
- Environmental Protection and Regulatory Compliance: Liners act as a barrier, preventing the leakage of potentially harmful substances into the surrounding environment. By containing and controlling the flow of oil, gas, and other substances, liners contribute significantly to environmental protection. This containment capability is vital in preventing soil and water contamination, which could otherwise result from leaks or seepage. Compliance with stringent environmental regulations and industry standards is facilitated by the use of robust and reliable liners, minimizing the environmental impact and ensuring responsible operation within the oil and gas industry.
- Cost-Effectiveness and Long-Term Sustainability: While the initial investment in liners may incur some cost, their use translates into long-term savings and sustainability. Liners, by protecting infrastructure from corrosion and wear, extend the lifespan of wells, pipelines, and storage facilities. This longevity reduces the need for frequent repairs or replacements, saving on maintenance costs in the long run. Additionally, their role in preventing leaks and spills helps in avoiding costly environmental cleanup operations and potential fines for non-compliance with environmental regulations. Ultimately, the integration of liners leads to a more sustainable and cost-effective operation in the oil and gas industry.
Exploring Various Types of Liners
- Casing Liners: Casing liners serve as a critical component in oil and gas wells, providing structural integrity and preventing the collapse of the borehole. These liners are typically installed within the wellbore and are instrumental in maintaining well stability and isolating various formations. Casing liners also act as a barrier against potential fluid migration between different geological layers, contributing to well safety and preventing environmental hazards. They come in various sizes and materials to suit different well conditions, depths, and pressure levels.
- Cement Liners: Cement liners play a pivotal role in securing the integrity of wellbores by providing a seal between the casing and the wellbore walls. These liners are installed through a process called cementing, which involves filling the annular space between the casing and the formation with cement slurry. This creates a robust barrier, preventing fluid migration and enhancing the overall structural stability of the well. Cement liners also aid in preventing the corrosion of metallic casings by isolating them from corrosive elements present in the surrounding environment.
- Tubing Liners: Tubing liners are utilized primarily in scenarios requiring additional tubing within the casing. These liners offer an extra layer of protection, particularly in environments where the casing might be subjected to high pressure, corrosive substances, or extreme temperatures. They help in controlling the flow of oil or gas from the reservoir to the surface, playing a crucial role in production optimization and well performance. Tubing liners are available in various sizes and materials, providing flexibility to cater to specific operational requirements.
- Liners for Specific Well Types (e.g., Horizontal, Vertical, Offshore): Different well configurations demand tailored liner solutions. For horizontal wells, liners are employed to address challenges related to maintaining wellbore stability and preventing collapse in the curved sections. Vertical wells often require various liners for different sections, adapting to geological variations. In offshore drilling, liners are designed to withstand harsh marine conditions, including saltwater corrosion and high-pressure environments. These specialized liners are engineered to ensure safety, longevity, and operational efficiency in unique offshore settings.
Key Challenges and Solutions in Liners
- Corrosion and Degradation Issues: One of the primary challenges faced in the realm of liners within the oil and gas industry is the persistent threat of corrosion and degradation. Exposure to harsh environmental conditions, varying temperatures, and the corrosive nature of the substances transported can deteriorate liners over time, potentially compromising their structural integrity. To address this, material science advancements have been pivotal. Innovations in corrosion-resistant materials, coatings, and protective layers have significantly improved the longevity and durability of liners, mitigating the impact of corrosion and enhancing their resilience against degradation.
- Compatibility and Material Selection: Selecting the appropriate materials for liners is crucial but often presents a significant challenge. Compatibility with the substances being transported, alongside the surrounding geological and operational conditions, is essential to prevent chemical reactions or material failure. Advanced research and development in material science have led to the creation of more compatible and resilient materials specifically designed for different applications. Additionally, detailed analysis and testing ensure that the chosen materials can withstand the intended environment and operational demands, reducing the risks associated with poor compatibility or material failure.
- Installation Complexities: Installing liners within oil and gas infrastructure, especially in complex well architectures or challenging environments, presents logistical and technical challenges. Ensuring proper installation, sealing, and structural integrity of liners is critical for their effective performance. Innovations in installation techniques, such as robotics, automated systems, and improved deployment methodologies, have simplified and streamlined the installation process. Additionally, the use of advanced monitoring tools and quality control measures during installation helps to identify and rectify potential issues early on, ensuring the liners are placed correctly and securely, minimizing the risk of operational failure.
Future Trends and Innovations
- Emerging trends in liner technology and materials: The future of liner technology is expected to witness a significant shift towards more resilient and sustainable materials. Innovations in nanotechnology, composite materials, and advanced polymers are gaining attention for their potential to enhance the durability and performance of liners. Engineers and researchers are exploring materials with improved resistance to corrosion, higher temperature tolerance, and better structural integrity to withstand harsh operational conditions in the oil and gas sector. This evolution aims to not only extend the lifespan of liners but also improve their overall effectiveness in ensuring well integrity and safety.
- Potential advancements in liner installation and maintenance practices: Advancements in liner installation methods are anticipated to streamline the process and enhance overall efficiency. Robotics and automated systems are being developed to reduce human intervention in installation, which can minimize errors and improve safety. Additionally, the use of smart tools and technologies for maintenance, such as self-diagnosing liners and predictive maintenance based on data analytics, holds the promise of reducing downtime and optimizing the lifespan of liners. Furthermore, the development of standardized installation protocols and best practices can contribute to increased reliability and cost-effectiveness in the long run.
- The role of digitalization and IoT in the future of liners in the industry: The integration of digitalization and the Internet of Things (IoT) is set to revolutionize the monitoring and management of liners in the oil and gas sector. IoT sensors embedded within liners allow real-time monitoring of various parameters, such as temperature, pressure, and structural integrity. This data can be transmitted and analyzed remotely, enabling proactive decision-making and predictive maintenance. Moreover, the utilization of digital twins – virtual replicas of physical liners – assists in simulating various operational scenarios and optimizing performance, thereby contributing to better decision-making and resource management for oil and gas companies. The amalgamation of digitalization and IoT is poised to redefine how liners are operated, maintained, and optimized in the industry.
Conclusion
From their diverse applications to the challenges they address, liners have continuously evolved, leveraging innovation and advanced technologies to meet the industry's demands. Their ability to mitigate risks, prevent corrosion, and enhance operational efficiency is undeniable. As the sector continues to push boundaries and explore new frontiers, liners stand as silent sentinels, ensuring the structural integrity of wells, protecting the environment, and complying with stringent regulations.
The future of liners in oil and gas appears promising, with ongoing advancements in material sciences, installation techniques, and the integration of digital solutions for remote monitoring and predictive maintenance. As the industry embraces these innovations, the potential for enhanced safety, cost-effectiveness, and sustainability grows significantly.
Popular Articles
Expand your knowledge with these insightful blog posts.
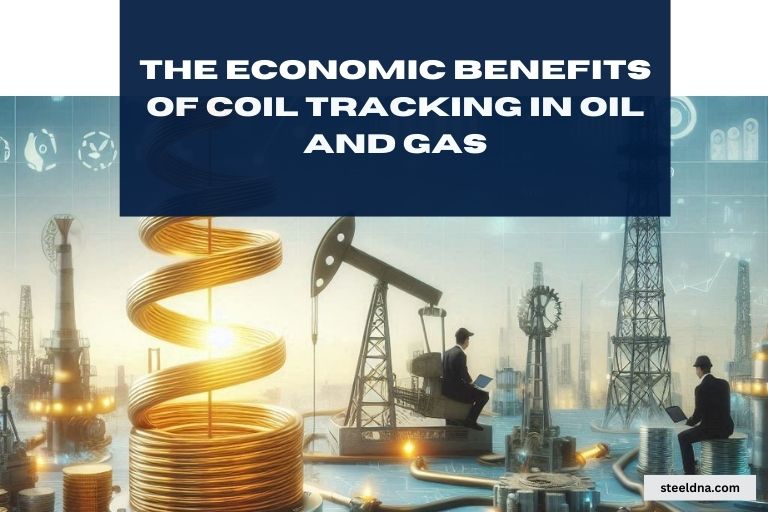
The Economic Benefits of Coil Tracking in Oil and Gas
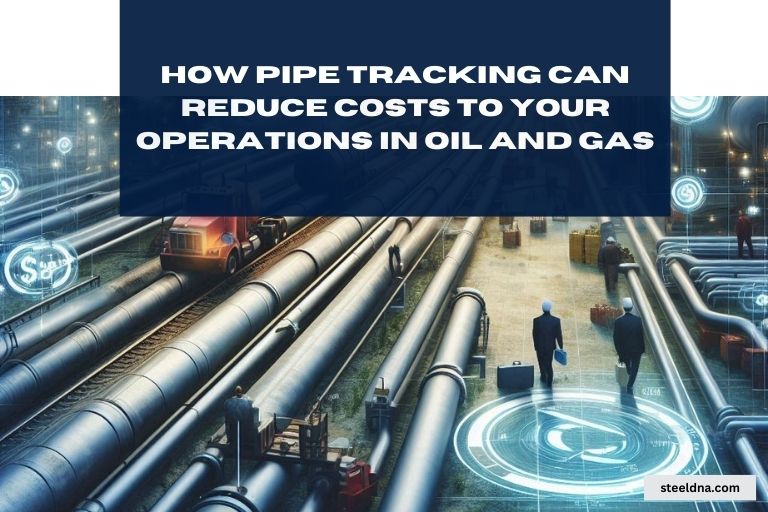
How Pipe Tracking Can Reduce Costs to your Operations in Oil and Gas
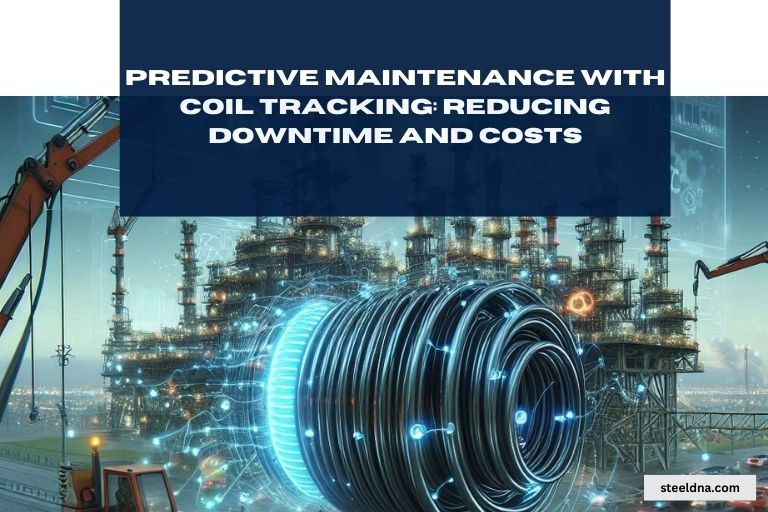
Predictive Maintenance with Coil Tracking: Reducing Downtime and Costs
Subscribe to our Blog
Welcome to our blog! Stay updated with the latest industry trends, tips, and insights. Subscribe now to never miss a post or contact us for collaborations and guest post opportunities.