Introduction to ERW (Electric Resistance Welded)
Picture this: a seamless integration of technology and craftsmanship, where metal meets precision through the magic of electric resistance welding. The process might seem arcane at first glance, but its implications reverberate across the the oil and gas sector and beyond. In this exploration, we will delve into the very heart of ERW, dissecting its welding process, understanding the anatomy of these pipes and uncovering the myriad applications that make them the unsung heroes of numerous industries.
Understanding ERW Welding Process
Electric Resistance Welding (ERW) is a sophisticated welding technique employed in the manufacturing of pipes. At its core, ERW involves the application of electrical currents to generate heat, fusing the edges of the metal sheets together. This process takes place without the use of any filler material, resulting in a seamless and robust joint. ERW welding is renowned for its efficiency and speed, making it a preferred method in various industries.
Overview of the ERW Welding Process
- Key Components Involved in ERW Welding- The ERW welding process relies on several key components to ensure precision and effectiveness. The primary elements include the electrodes, which transmit the electrical current, and the rollers, responsible for guiding and shaping the metal sheets. Additionally, a power source provides the necessary energy for the welding operation. Understanding these components is crucial to appreciating the intricacies of the ERW process and its ability to produce high-quality, consistent welded pipes.
- Comparison with Other Welding Methods- In comparison to traditional welding techniques, ERW offers distinct advantages. Unlike cumbersome methods that require filler materials, ERW creates joints by melting and bonding the actual edges of the metal sheets. This results in a stronger, more durable connection. Moreover, the absence of open flames or the need for flux makes ERW a cleaner and more environmentally friendly option.
- Advantages of ERW over Traditional Welding Techniques- The advantages of ERW welding extend beyond its fundamental process. The absence of filler materials not only reduces costs but also minimizes the risk of defects in the welded joint. ERW is highly automated, leading to increased production efficiency and consistency. Additionally, the controlled heat input in ERW reduces the likelihood of distortions and residual stresses in the pipes, contributing to their structural integrity. These advantages position ERW as a cost-effective, high-quality welding method with broad applications across diverse industries.
- Limitations and Challenges- While ERW has numerous advantages, it's essential to acknowledge its limitations and challenges. Thin-walled pipes can be more challenging to produce using ERW, and the process may not be suitable for materials with high alloy content. Additionally, achieving a flawless weld can be affected by factors such as surface contamination, leading to potential defects. Understanding these challenges is critical in making informed decisions about the applicability of ERW in specific manufacturing scenarios.
Step-by-Step Process of ERW Pipe Production
- Forming the Pipe- In the initial step of ERW pipe production, raw material – typically coils of steel – undergoes a forming process. This involves shaping the flat strip into a cylindrical form. The steel coil is gradually transformed through a series of rollers, adjusting its shape to match the desired pipe dimensions. Precision in this stage is critical to ensure uniformity and strength in the final product. The forming process sets the foundation for the subsequent welding and sizing steps, emphasizing the importance of accurate shaping for a high-quality ERW pipe.
- Welding- The welding phase is at the heart of the ERW process. Electric resistance welding occurs as the edges of the formed steel strip are heated to the point of fusion. This is achieved by passing a high-frequency electric current through the metal. As the edges come together, a weld is formed, creating a seamless bond along the length of the pipe. Control over the welding parameters is crucial to maintain the integrity of the joint, and advancements in technology have allowed for increased precision, efficiency, and consistency in this critical stage of ERW pipe production.
- Sizing and Straightening- Following the welding process, the newly formed pipe undergoes sizing and straightening to meet specific dimensional requirements. Sizing involves reducing the diameter of the pipe to the desired dimensions through a series of rollers or stretch-reducing mills. Simultaneously, the pipe is straightened to eliminate any distortions or bends that may have occurred during welding. This stage ensures that the ERW pipe meets the precise specifications required for its intended application, guaranteeing uniformity and structural integrity.
- Cut to Length- Once the ERW pipe has been properly sized and straightened, it is cut to the required length. Precision in this step is paramount, as it determines the final product's usability in various applications. Modern ERW manufacturing facilities are equipped with advanced cutting mechanisms to achieve accurate and consistent lengths, contributing to the efficiency and cost-effectiveness of the overall production process.
- Testing and Inspection- Quality assurance is a fundamental aspect of ERW pipe production. The final step involves rigorous testing and inspection to ensure that the pipes meet industry standards and specifications. Non-destructive testing methods, such as ultrasonic or eddy current testing, are commonly employed to detect any defects or irregularities in the weld or pipe structure. This meticulous quality control process guarantees that the ERW pipes meet the required performance criteria, providing confidence to end-users in diverse industries.
Quality Control and Testing
Quality control and testing are paramount ensuring that these critical components meet rigorous standards for reliability and durability. Rigorous quality control measures are implemented throughout the manufacturing process to identify and rectify any defects that may compromise the structural integrity of the pipes. Non-destructive testing methods, such as ultrasonic testing and eddy current testing, play a pivotal role in detecting imperfections, cracks or irregularities invisible to the naked eye. Compliance with industry standards and regulations is meticulously maintained to guarantee that the ERW pipes not only meet but often exceed the expectations of various sectors, including oil and gas, construction, and automotive. This commitment to quality control not only safeguards the end-users but also enhances the reputation of ERW pipes as a trusted and dependable solution in demanding applications.
Conclusion to ERW (Electric Resistance Welded)
The efficiency, cost-effectiveness, and environmental considerations make ERW an attractive choice for applications in oil and gas. The electric resistance welding process, with its meticulous steps from forming to testing, ensures a high level of quality and consistency in the production of ERW pipes. The advantages of this method, such as its versatility and adherence to industry standards, position it as a reliable and sustainable solution for the challenges posed by traditional welding techniques. With sustainability, efficiency, and versatility in its arsenal, ERW technology stands ready to shape the pipelines and structures of tomorrow, contributing to a resilient and dynamic industrial landscape.
Popular Articles
Expand your knowledge with these insightful blog posts.
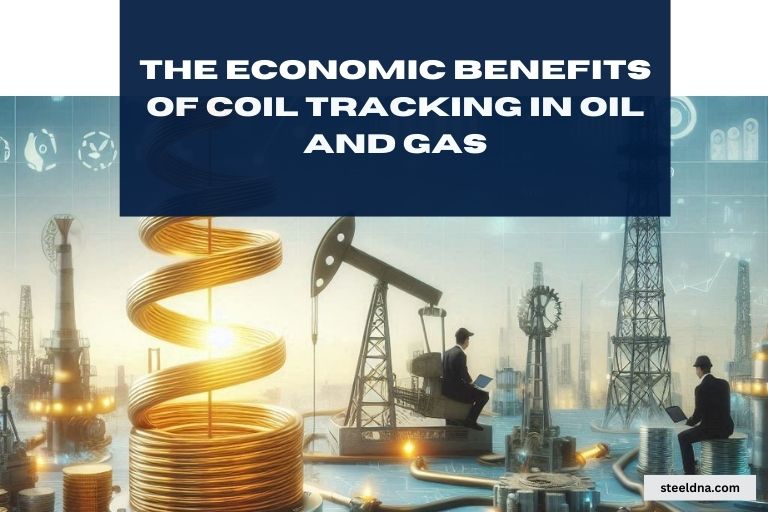
The Economic Benefits of Coil Tracking in Oil and Gas
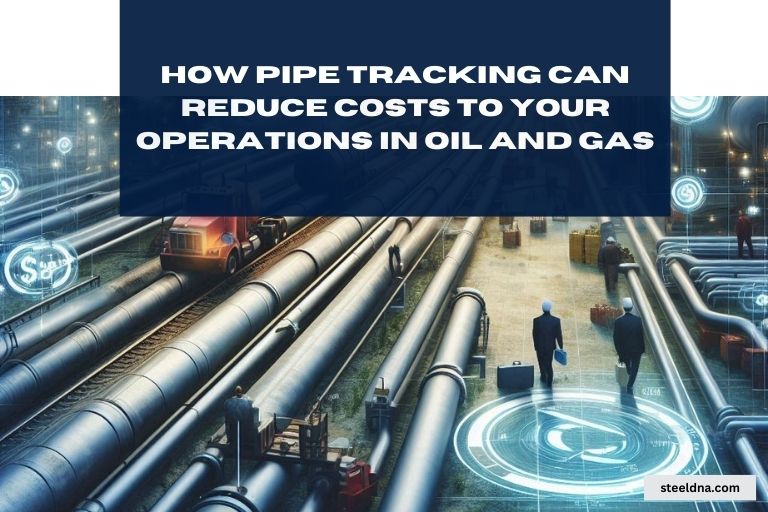
How Pipe Tracking Can Reduce Costs to your Operations in Oil and Gas
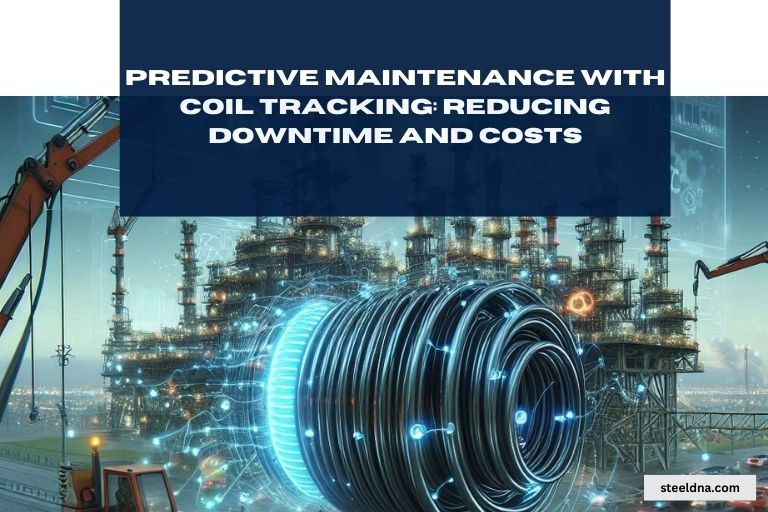
Predictive Maintenance with Coil Tracking: Reducing Downtime and Costs
Subscribe to our Blog
Welcome to our blog! Stay updated with the latest industry trends, tips, and insights. Subscribe now to never miss a post or contact us for collaborations and guest post opportunities.